Größer, höher, leistungsstärker – und schwerer: Die Entwicklung von Windenergieanlagen kennt nur die Richtung nach oben. 2012 brachte es eine neu errichtete Durchschnittsanlage laut Auswertung der Deutschen Windguard auf eine Leistung von 2,4 MW und einen Rotordurchmesser von 99 Metern. Zehn Jahre später hat sich die Leistung auf 4,4 MW nahezu verdoppelt und die Turbinen erreichen Rotordurchmesser von 150 Metern.
„Rotorblätter, die über 70 Meter lang sind, müssen im Betrieb enorme Lasten aushalten“, sagt Professor Clemens Jauch vom Institut für Windenergietechnik der Hochschule Flensburg. „Entsprechend hoch ist ihr Gewicht und entsprechend groß sind die Lasten, die über den Turm und das Fundament abgeleitet werden müssen. Und das wiederum sorgt für einen enormen Verbrauch von Beton und Stahl für Fundament und Turm.“ 1.000 Kubikmeter Beton können für ein Fundament benötigt werden, mehrere 100 Tonnen Stahl für den Turm, der damit zwischen 15 und 25 Prozent der Kosten einer gesamten Windenergieanlage ausmacht.
Kosten, die angesichts knapper Ressourcen und steigender CO2-Preise künftig noch mehr ins Gewicht fallen dürften. Wie also lässt sich Material einsparen, ohne dass die Stabilität oder der Ertrag beeinträchtigt werden?
Diese Frage stellte sich ein Team der Hochschule Flensburg und entwickelte gemeinsam mit dem Windenergieanlagenentwickler Aerovide(ehemals Aerodyn) und dem Hydraulikhersteller Hydac ein Schwungradspeichersystem, das Fluidmassen in den Rotorblätter so einsetzt, dass sich die Massenträgheiten der Rotorblätter variieren lassen und mechanische Lasten auf Turm und Fundament reduziert werden können.
Ursprünglich hatten die Wissenschaftler um Jauch die Idee verfolgt, mit Hilfe des Schwungradspeichers Netzdienstleistungen erbringen zu können. Doch im Laufe der Zeit rückte ein Nebenaspekt immer mehr in den Fokus der Forschenden: Die Ressourceneffizienz, die sich durch die dynamischen Fluidmassen erreichen ließ. „Wir können mit unserem System die Belastungen in der Tragstruktur der Windenergieanlage deutlich verringern“, erläutert Jauch.
Das Ganze funktioniert so: Der Schwungradspeicher besteht in jedem Rotorblatt aus mindestens zwei hydropneumatischen Kolbenspeichern, mindestens einem nahe der Blattspitze und einem in der Blattwurzel. Das Fluidvolumen in dem System ist an die Leistung der Windenergieanlage angepasst und kann bei einer Vier-Megawatt-Anlage rund 900 Liter Wasser-Glykol-Gemisch pro Blatt betragen. Die Speicher sind über eine Leitung verbunden. Per Regler lassen sich Ventile und Pumpen so steuern, dass die Flüssigkeit je nach Bedarf von Kolbenspeicher zu Kolbenspeicher verschoben wird.
„Unsere Bedingung war, dass wir mit dem Einbau der Kolbenspeicher keine zusätzlichen Massen in die Rotorblätter bringen“, erklärt Jauch die Herausforderung. „Deshalb mussten sie an anderer Stelle eingespart werden.“ Also ersetzte das Forschungsteam Material in den Gurten der Rotorblätter teilweise durch die Materialien der Kolbenspeicher, die aus einer dünnen Schicht Stahl und kohlefaserverstärktem Kunststoff bestehen. „Die Komponenten des Schwungradspeichers werden zum integralen Bestandteil der Tragstruktur des Rotorblattes, es wird dadurch kaum schwerer“, so Jauch.
Und was bringt das Ganze im Anlagenbetrieb? „Wir können eine ganze Reihe von lastverringernden Funktionalitäten mit unserem Schwungradspeicher realisieren“, sagt Jauch. „So können wir beispielsweise Resonanzen verhindern. Das heißt, wir können verhindern, dass sich die Schwingungen etwa eines Rotorblattes zu sehr aufschaukeln – und dieses zu schnell ermüdet.“ Dies gelingt, indem der Schwungradspeicher abhängig von der Drehzahl gefahren wird. Bei einer gegebenen Drehzahl kann die Eigenfrequenz der Rotorblätter mit der verschiebbaren Masse des Schwungradspeichers um bis zu 14 Prozent verändert werden, so dass diese Anregung nicht zu schädlichen Schwingungen in den Rotorblättern führt.
Besonders deutlich würden die Vorteile des Schwungradspeichers, wenn die Windenergieanlage eine Notbremsung ausführen muss, zum Beispiel wenn das Netz ausfällt, die Maschine aber unter Last läuft, sagt Jauch: „Eine Notbremsung ist eine Extrembelastung für eine Windenergieanlage.“ Zum einen beschleunige der Triebstrang, wenn der Generator keine Leistung mehr ins Netz einspeisen könne. „Der Pitchwinkel, über den die Anlage gebremst wird, kann nicht so schnell verfahren werden. Es kann deshalb zu Überdrehzahlen mit gefährlichen Zentrifugalkräften kommen.“ Das zweite Problem: Das Verstellen des Pitchwinkels sorgt für eine große Veränderung des aerodynamischen Schubs bis hin zur Schubumkehr. Hier kann der Schwungradspeicher abmildern: „Wir haben Notbremsungen simuliert, einmal mit, einmal ohne Schwungradspeicher und konnten die Überdrehzahl um acht Prozent und die Schubveränderung um 18 Prozent reduzieren“, berichtet der Professor.
Auch Rotorunwuchten, die im schlimmsten Fall dafür sorgen, dass die Anlage in der Turmfrequenz quer schwingt, ließen sich mit dem Schwungradspeicher vermeiden. „Weitere Anwendungsfälle sind Leistungsverstetigung im Betrieb nahe der Nennleistung und die Verringerung der negativen Dämpfung des Triebstrangs im Volllastbetrieb sowie Verringerung der Anregung durch Gravitation und Windscherung“, so Jauch.
Allerdings: Eine Nachrüstlösung ist das System des Schwungradspeichers nicht. Die komplette Windenergieanlage wird inklusive der Rotorblätter designt und eine entsprechende Regelung integriert. „Wir wollen im Sommer in die zweite Phase unseres Forschungsprojekts starten“, berichtet Jauch. Dann wollen die Wissenschaftler die Funktionalität und das Blattdesign für unterschiedliche Anlagenkategorien von einer Offshore-Starkwindanlage über eine typische „Brot-und-Butter“-Turbine bis zu einer Schwachwindanlage mit besonders hohem Turm und großem Rotor anpassen. „Wir wollen sehen, für welchen Typ der Schwungradspeicher am meisten Einsparung bringt. Dann können wir anhand von Konzeptdesigns auch sagen, wie viel Material konkret eingespart wird“, kündigt der Professor an.
Die Reaktion der Anlagenhersteller allerdings fällt bislang zurückhaltend aus. „Die Hersteller sind eher darauf konzentriert, ihre bestehenden Anlagendesigns auf Kosteneinsparung zu optimieren“, so Jauch. Doch er ist zuversichtlich, dass die Technologie eine Chance hat. Die Themen Ressourceneffzienz und CO2-Fußabdruck werden immer wichtiger, nicht nur für Akzeptanz und Wirtschaftlichkeitsberechnungen, sondern auch als Vergabekriterium bei öffentlichen Ausschreibungen. „Mit den heute gängigen Anlagentechnologien gibt es da nicht mehr viel Einsparpotenzial“, so Jauch.
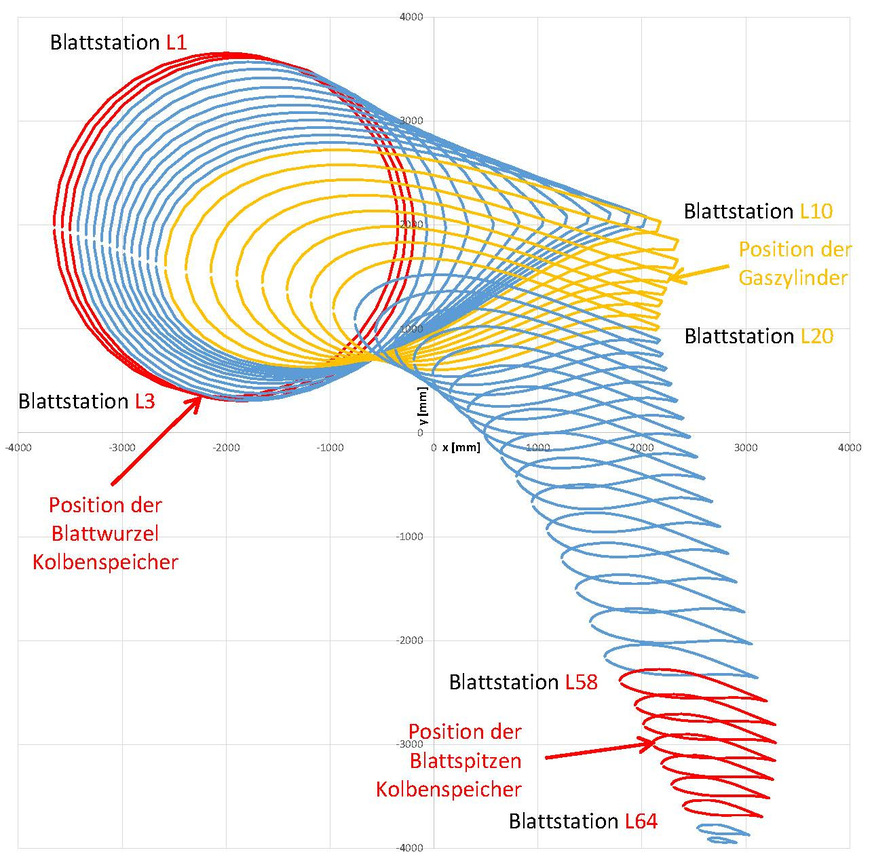
WETI